Jak projektować części plastikowe
Krótki opis:
Do projektowanie części z tworzyw sztucznychto określenie kształtu, rozmiaru i precyzji części, w oparciu o rolę, jaką odgrywają w produkcie, oraz zasady procesu formowania tworzywa sztucznego. Końcowym wynikiem są rysunki dotyczące produkcji formy i części z tworzywa sztucznego.
Produkcja produktu zaczyna się od projektu. Projektowanie części z tworzyw sztucznych bezpośrednio determinuje realizację struktury wewnętrznej, koszt i funkcję produktu, a także określa kolejny etap produkcji formy, koszt i cykl, a także proces i koszt formowania wtryskowego i postprodukcji.
Części plastikowe są szeroko stosowane w różnych produktach, obiektach i życiu ludzi we współczesnym społeczeństwie. Części plastikowe wymagają różnych kształtów i funkcji. Wykorzystują tworzywa sztuczne, a ich właściwości są zróżnicowane. Jednocześnie istnieje wiele sposobów wytwarzania części z tworzyw sztucznych w przemyśle. Zatem projektowanie części z tworzyw sztucznych nie jest prostą pracą.
Różne projekty części i materiały są wytwarzane w różnych procesach. Przetwarzanie do formowania tworzyw sztucznych obejmuje głównie:
1. formowanie wtryskowe
2. formowanie dmuchane
3. formowanie tłoczne
4. formowanie obrotowe
5. termoformowanie
6. wytłaczanie
7. fabrykacja
8. spienianie
Istnieje wiele sposobów ich masowej produkcji. Formowanie wtryskowe jest popularną metodą produkcji, ponieważ formowane wtryskowo 50% ~ 60% części z tworzyw sztucznych są wytwarzane przez formowanie wtryskowe, jest to zdolność produkcyjna z dużą prędkością.
Prezentacja niektórych zaprojektowanych przez nas plastikowych części:
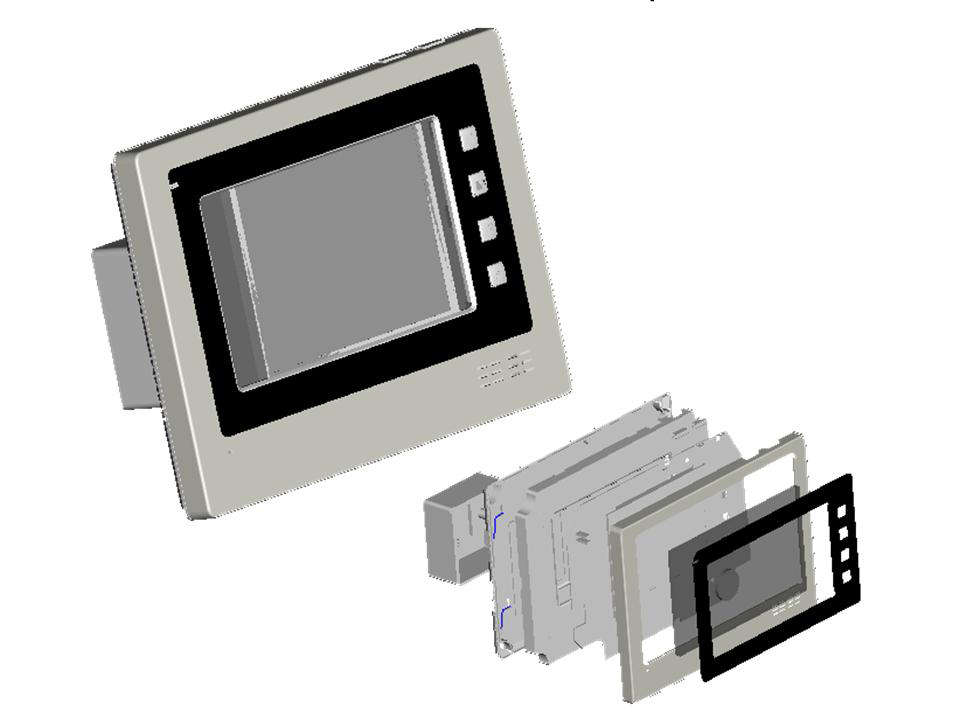
Plastikowa obudowa telefonu wizyjnego
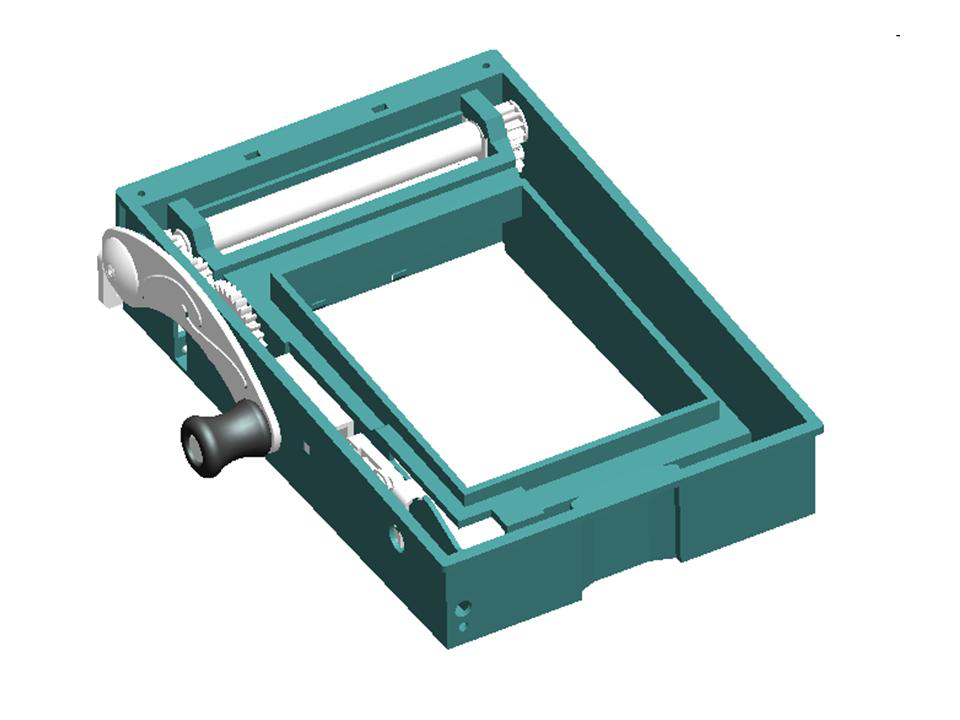
Plastikowe części mechanizmu
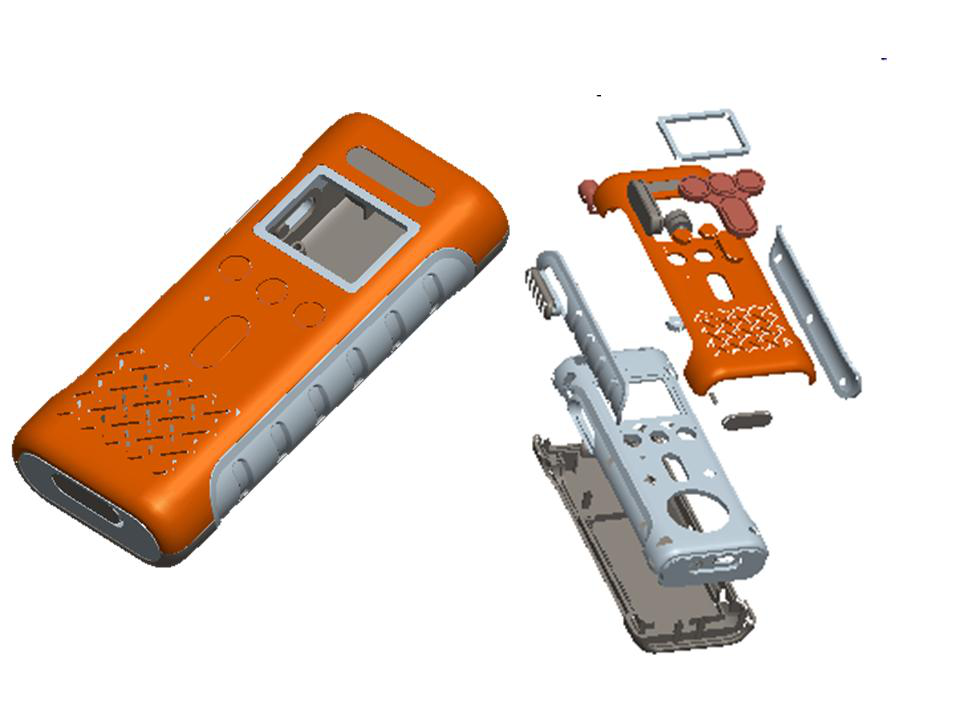
Plastikowe skrzynki elektroniczne
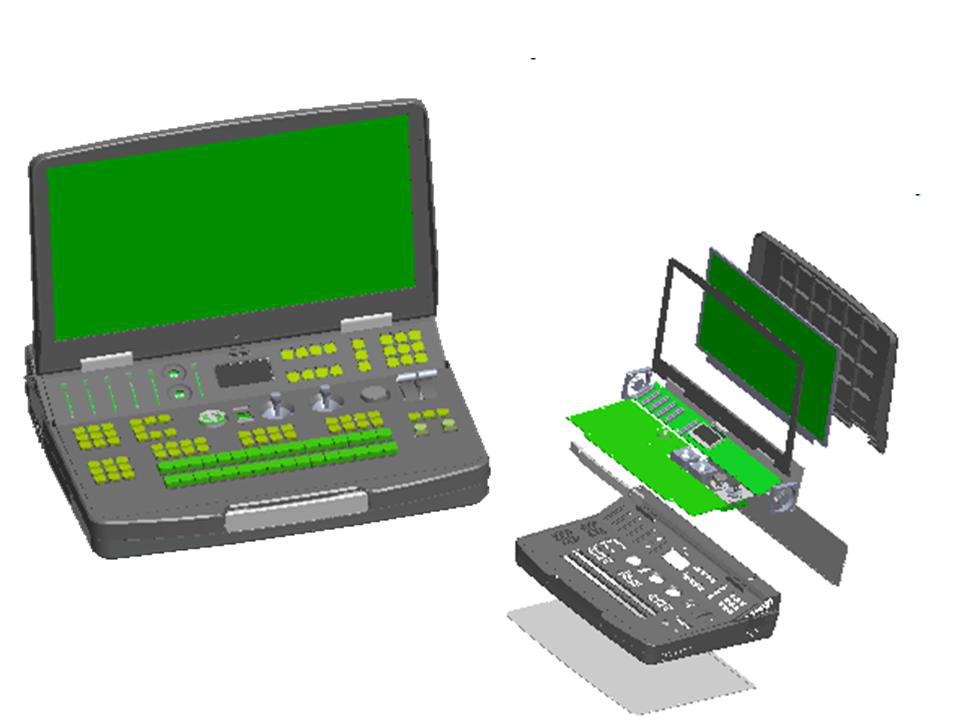
Plastikowa obudowa na instrument
Poniżej przedstawiamy szczegółowo, jak projektować części z tworzyw sztucznych w trzech aspektach
* 10 wskazówek dotyczących projektowania części z tworzyw sztucznych, które musisz znać
1. Określić wygląd i rozmiar produktu.
To pierwszy krok w całym procesie projektowania. Zgodnie z badaniami rynku i wymaganiami klientów określ wygląd i funkcję produktów oraz formułuj zadania związane z rozwojem produktu.
Zgodnie z zadaniem programistycznym zespół programistów przeprowadza techniczną i technologiczną analizę wykonalności produktu oraz buduje trójwymiarowy model wyglądu produktu. Następnie zgodnie z realizacją funkcji i montażem produktu planowane są możliwe części.
2. Oddziel poszczególne części od rysunków produktów, wybierz typ żywicy z tworzywa sztucznego do części z tworzywa sztucznego
Ten krok polega na oddzieleniu części od modelu 3D uzyskanego w poprzednim kroku i zaprojektowaniu ich jako indywidualnych. Zgodnie z wymaganiami funkcjonalnymi części, wybierz odpowiednie tworzywa sztuczne lub materiały okucia. Na przykład ABS jest zwykle używany w
obudowa, ABS / BC lub PC muszą mieć określone właściwości mechaniczne, przezroczyste części, takie jak klosz, słupek lampy z PMMA lub PC, osprzęt lub części zużywające się z POM lub Nylon.
Po wybraniu materiału części można przystąpić do projektowania szczegółowego.
3. Zdefiniuj kąty pochylenia
Kąty pochylenia pozwalają na wyjęcie tworzywa z formy. Bez kątów pochylenia część stawiałaby znaczny opór z powodu tarcia podczas usuwania. Kąty pochylenia powinny występować po wewnętrznej i zewnętrznej stronie części. Im głębsza część, tym większy kąt pochylenia. Prosta praktyczna zasada mówi, że kąt pochylenia wynosi 1 stopień na cal. Niewystarczający kąt pochylenia może skutkować zadrapaniami wzdłuż boków części i / lub dużymi śladami sworznia wypychacza (więcej o tym później).
Kąty pochylenia powierzchni zewnętrznej: im głębsza część, tym większy kąt pochylenia. Prosta praktyczna zasada mówi, że kąt pochylenia wynosi 1 stopień na cal. Niewystarczający kąt pochylenia może skutkować zadrapaniami wzdłuż boków części i / lub dużymi śladami sworznia wypychacza (więcej o tym później).
Zwykle, aby uzyskać dobry wygląd powierzchni, na powierzchni części tworzy się teksturę. Ściana z fakturą jest chropowata, tarcie duże i nie jest łatwo usunąć ją z wnęki, dlatego wymaga większego kąta ciągnienia. Im grubsza tekstura, tym większy wymagany kąt rysowania.
4. Zdefiniuj grubość ścianki / jednolitą grubość
Formowanie w postaci litej nie jest pożądane w formowaniu wtryskowym z następujących powodów:
1) .Czas chłodzenia jest proporcjonalny do kwadratu grubości ściany. Długi czas chłodzenia ciała stałego zniweczy ekonomię masowej produkcji. (słaby przewodnik ciepła)
2) Grubsza sekcja skurczy się bardziej niż cieńsza, co powoduje zróżnicowany skurcz, powodując wypaczenie lub zapadnięcie się itp. (Charakterystyka skurczu tworzyw sztucznych i właściwości pvT)
Dlatego mamy podstawową zasadę projektowania części z tworzyw sztucznych; w miarę możliwości grubość ścianki powinna być jednolita lub stała na całej części. Ta grubość ścianki nazywana jest nominalną grubością ścianki.
Jeśli w części znajduje się jakaś pełna sekcja, należy ją wydrążać przez wprowadzenie rdzenia. Powinno to zapewnić jednakową grubość ścianki wokół rdzenia.
3) Jakie są czynniki brane pod uwagę przy decydowaniu o grubości ściany?
Musi być wystarczająco gruby i sztywny do tego zadania. Grubość ścianki może wynosić od 0,5 do 5 mm.
Musi być również wystarczająco cienki, aby chłodzić szybciej, co skutkuje mniejszą wagą części i wyższą produktywnością.
Wszelkie odchylenia w grubości ścian powinny być jak najmniejsze.
Część z tworzywa sztucznego o różnej grubości ścianki będzie podlegać różnym szybkościom chłodzenia i różnemu skurczowi. W takim przypadku osiągnięcie wąskiej tolerancji staje się bardzo trudne, a często niemożliwe. Tam, gdzie istotna jest zmiana grubości ścian, przejście między nimi powinno być stopniowe.
5.Projekt połączeń między częściami
Zwykle musimy połączyć ze sobą dwie powłoki. Aby utworzyć zamknięte pomieszczenie między nimi, aby umieścić elementy wewnętrzne (zespół PCB lub mechanizm).
Typowe typy połączeń:
1). Karabińczyki:
Połączenie karabińczyka jest powszechnie stosowane w produktach małych i średnich rozmiarów. Charakteryzuje się tym, że karabińczyki są zwykle umieszczane na krawędziach części, a rozmiar produktu można zmniejszyć. Po zmontowaniu jest zamykany bezpośrednio bez użycia narzędzi takich jak śrubokręt, zgrzewarka ultradźwiękowa i inne. Wadą jest to, że karabińczyki mogą bardziej skomplikować pleśń. Mechanizm suwaka i mechanizm podnoszący są potrzebne do wykonania połączenia karabińczyka i zwiększenia kosztu formy.
2). Połączenia śrubowe:
Połączenia śrubowe są mocne i niezawodne. W szczególności mocowanie śruba + nakrętka jest bardzo niezawodne i trwałe, umożliwiając wielokrotny demontaż bez pęknięć. Połączenie śrubowe jest odpowiednie dla produktów o dużej sile blokowania i wielokrotnym demontażu. Wadą jest to, że kolumna śrubowa zajmuje więcej miejsca.
3). Bossowie montażowe:
Połączenie występów montażowych polega na zamocowaniu dwóch części poprzez ścisłą koordynację między występami i otworami. Ten sposób połączenia nie jest wystarczająco mocny, aby umożliwić demontaż produktów. Wadą jest to, że siła blokowania zmniejsza się wraz ze wzrostem czasu demontażu.
4). Spawanie ultradźwiękowe:
Zgrzewanie ultradźwiękowe polega na umieszczeniu dwóch części w formie ultradźwiękowej i stopieniu powierzchni styku pod działaniem zgrzewarki ultradźwiękowej. Rozmiar produktu może być mniejszy, forma wtryskowa jest stosunkowo prosta, a połączenie jest mocne. Wadą jest zastosowanie formy ultradźwiękowej i zgrzewarki ultradźwiękowej, wielkość produktu nie może być zbyt duża. Po demontażu części ultradźwiękowych nie można ponownie użyć.
6. podcięcia
Podcięcia to elementy, które przeszkadzają w usunięciu jednej z połówek formy. Podcięcia mogą pojawić się w dowolnym miejscu projektu. Są one równie niedopuszczalne, jeśli nie gorsze niż brak kąta pochylenia części. Jednak pewne podcięcia są konieczne i / lub nieuniknione. W takich przypadkach konieczne
podcięcia powstają w wyniku przesuwania / przesuwania części w formie.
Należy pamiętać, że tworzenie podcięć jest bardziej kosztowne podczas produkcji formy i należy je ograniczyć do minimum.
7. wsparcie żeber / klinów
Żebra w części z tworzywa sztucznego poprawiają sztywność (zależność między obciążeniem a ugięciem części) części i zwiększają sztywność. Zwiększa również zdolność do formowania, ponieważ przyspieszają przepływ stopu w kierunku żebra.
Żebra są umieszczane wzdłuż kierunku maksymalnego naprężenia i ugięcia na niewidocznych powierzchniach części. Wypełnienie formy, skurcz i wypychanie powinny również wpływać na decyzje dotyczące umieszczenia żeber.
Żebra, które nie łączą się z pionową ścianą, nie powinny kończyć się gwałtownie. Stopniowe przejście na ścianę nominalną powinno zmniejszyć ryzyko koncentracji naprężeń.
Żebro - wymiary
Żebra powinny mieć następujące wymiary.
Grubość żebra powinna wynosić od 0,5 do 0,6 nominalnej grubości ściany, aby uniknąć zapadnięcia się.
Wysokość żebra powinna być 2,5 do 3 razy większa od nominalnej grubości ściany.
Żebro powinno mieć kąt pochylenia 0,5 do 1,5 stopnia, aby ułatwić wyrzut.
Podstawa żebra powinna mieć promień 0,25 do 0,4 razy nominalną grubość ścianki.
Odległość między dwoma żebrami powinna wynosić 2 do 3 razy (lub więcej) nominalnej grubości ścianki.
8. promieniste krawędzie
Kiedy spotykają się dwie powierzchnie, tworzy róg. W narożniku grubość ściany wzrasta do 1,4-krotności nominalnej grubości ściany. Powoduje to zróżnicowany skurcz i naprężenia wtłaczane oraz dłuższy czas chłodzenia. Dlatego ryzyko awarii podczas obsługi wzrasta na ostrych zakrętach.
Aby rozwiązać ten problem, rogi należy wygładzić promieniem. Promień należy podać zarówno zewnętrznie, jak i wewnętrznie. Nigdy nie używaj wewnętrznego ostrego narożnika, ponieważ sprzyja pękaniu. Promień powinien być taki, aby potwierdzał zasadę stałej grubości ściany. Zaleca się mieć promień 0,6 do 0,75 grubości ściany w rogach. Nigdy nie używaj wewnętrznego ostrego narożnika, ponieważ sprzyja pękaniu.
9. projekt łba śruby
Zawsze używamy śrub do łączenia dwóch półkul lub mocowania PCBA lub innych komponentów do plastikowych części. Tak więc piasty śrubowe są strukturą do wkręcania i stałych części.
Piasta śruby ma kształt cylindryczny. Boss może być połączony u podstawy z częścią macierzystą lub może być połączony z boku. Łączenie z boku może skutkować grubym przekrojem tworzywa sztucznego, co nie jest pożądane, ponieważ może powodować zapadanie się i wydłużać czas chłodzenia. Ten problem można rozwiązać, łącząc wypukłość przez żebro ze ścianą boczną, jak pokazano na szkicu. Puszka może być usztywniona poprzez zastosowanie żeber przyporowych.
Śruba służy do mocowania innej części na piaście. Istnieją śruby typu gwintowania i śruby typu tnącego bieżnik. Wkręty samoformujące gwint są stosowane na tworzywach termoplastycznych, a wkręty do gwintowania są stosowane na nieelastycznych termoutwardzalnych częściach z tworzywa sztucznego.
Wkręty samoformujące gwinty wytwarzają gwint wewnętrzny na wewnętrznej ściance piasty w wyniku płynięcia na zimno - tworzywo sztuczne jest raczej lokalnie odkształcane niż cięte.
Piasta śruby musi mieć odpowiednie wymiary, aby wytrzymać siły wkręcania śruby i obciążenie działające na śrubę.
Rozmiar otworu w stosunku do śruby ma kluczowe znaczenie dla odporności na zdzieranie gwintu i wyciąganie śruby.
Zewnętrzna średnica piasty powinna być wystarczająco duża, aby wytrzymać naprężenia obręczy spowodowane wygniataniem gwintów.
Otwór ma nieco większą średnicę we wnęce wejściowej na krótkiej długości. Pomaga to w ustaleniu położenia śruby przed wkręceniem. Zmniejsza również naprężenia na otwartym końcu piasty.
Producenci polimerów podają wytyczne dotyczące określania wymiarów piasty dla ich materiałów. Producenci śrub również podają wytyczne dotyczące właściwego rozmiaru otworu dla śruby.
Należy zwrócić uwagę, aby zapewnić mocne połączenia spawane wokół otworu na śrubę w piaście.
Należy uważać, aby uniknąć uformowanego stresu w szefie, ponieważ może on zawieść w agresywnym środowisku.
Otwór w piaście powinien być głębszy niż głębokość gwintu.
10. dekoracja powierzchni
Czasami, aby uzyskać ładny wygląd, często wykonujemy specjalną obróbkę powierzchni plastikowej obudowy.
Takich jak: tekstura, wysoki połysk, malowanie natryskowe, grawerowanie laserowe, tłoczenie na gorąco, galwanizacja i tak dalej. Konieczne jest uwzględnienie w projektowaniu produktu z wyprzedzeniem, aby uniknąć nieosiągnięcia późniejszego przetwarzania lub zmian wielkości wpływających na montaż produktu.